Charlie Wittich lives with his wife and two children in a Grade 2 Listed (applies to whole house), 4 bed house in the Littlebury Conservation Area. The house is in 3 sections – an original 1560 part fronting the high street and mid-1800’s and mid-1900’s extensions.
The house had a very old oil boiler when they moved in. In 2019 their regular service engineer advised that they should look into getting either a new oil boiler, or alternative heating system, because spare parts were becoming obsolete. With increasing fluctuations in oil prices, and the house being old, single glazed and not well insulated, the future options were a challenge. Charlie knew about ASHP’s from his work in property services, so investigated them online and found an agency high on the web search that would assess his house’s suitability and organise installation. He also researched ASHP’s via his work contacts. He used a young company to manage the project, at the time known as Project Air Source (PAS, https://www.facebook.com/projectairsource/?locale=en_GB).
A PAS representative visited, thoroughly explained the ASHP technology and the benefits of switching to fully electric heating. PAS managed the project, including the necessary pre-requisites (as detailed below) and identified a company to supply the ASHP. This ASHP company in turn contracted local installers to install the unit and associated parts.
Actions required before the unit could be installed (organised by PAS):
1. Satisfy the government criteria at the time for homes with ASHP. All 3 roof spaces required a lot of additional loft insulation and were filled with as much lagging as possible.
2. Any single panel radiators were replaced with double ones, which radiate heat much more effectively.
3. An Energy Performance Certificate (EPC) was required and was issued after the insulation work was done. Initially the rating was F but is now E after insulation, etc. Charlie was advised might possibly become a D if all the windows had secondary double glazing.
4. An electrician assessed the two Electrical Consumer Units (ECU’s) in the house to ensure they complied with the latest safety regulation and were compatible with the ASHP installation.
5. Once the ECUs had been checked, UK Power Networks had to attend to increase the electrical capacity in the property from 60amps to 100amps to ensure it could cope with the increased electrical draw from the ASHP.
All of the above stages ran smoothly and all parties involved were very professional. Not so point 6.
6. Listed Building Consent (LBC) was required. PAS had an in-house planning dept and liaised with the local council as part of their service. In an initial informal conversation with the planning department, Charlie was informed that the process would be straight forward and free to obtain LBC. Unfortunately, it proved not to be quick, easy or free! The actual timeframe resulted in delayed installation by approximately 2 months, and approximately £1,000 administration charges to obtain the LBC, plus an approximate £400 to buy and install a wooden louvered screen to surround the ASHP, required by the council’s Conservation team for ‘aesthetic and noise reduction purposes’, despite the low noise output and the position of the ASHP being secluded from neighbours and the roadside. Charlie had to arrange a meeting with the then head of the planning department in order to get them to co-ordinate the necessary internal departments to liaise, expedite and finalise the matter.
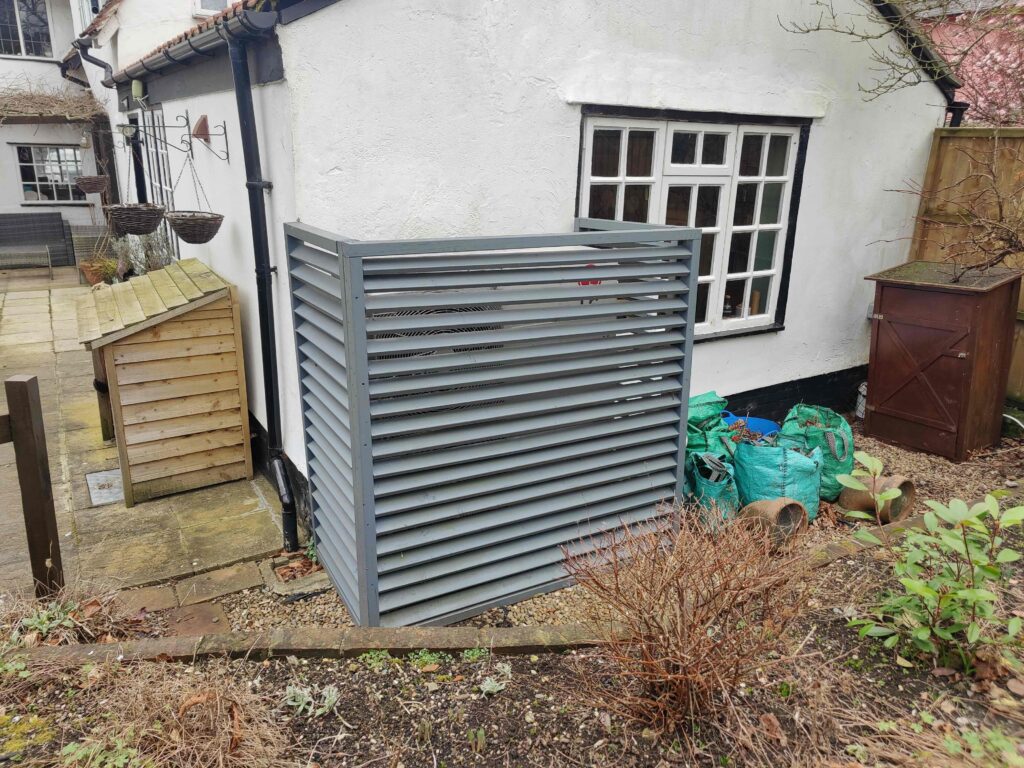
Note: This is an area where Littlebury Energy Project are now working with Uttlesford District Council to improve the planning process for listed and other buildings in the conservation area.
ASHP unit and installation
The ASHP manufacturer was LG. The specific unit selected as the most appropriate model was the THERMA V https://www.lg.com/uk/air-to-water-heat-pumps/. This comes with a 10 year warranty for the ASHP and associated parts.
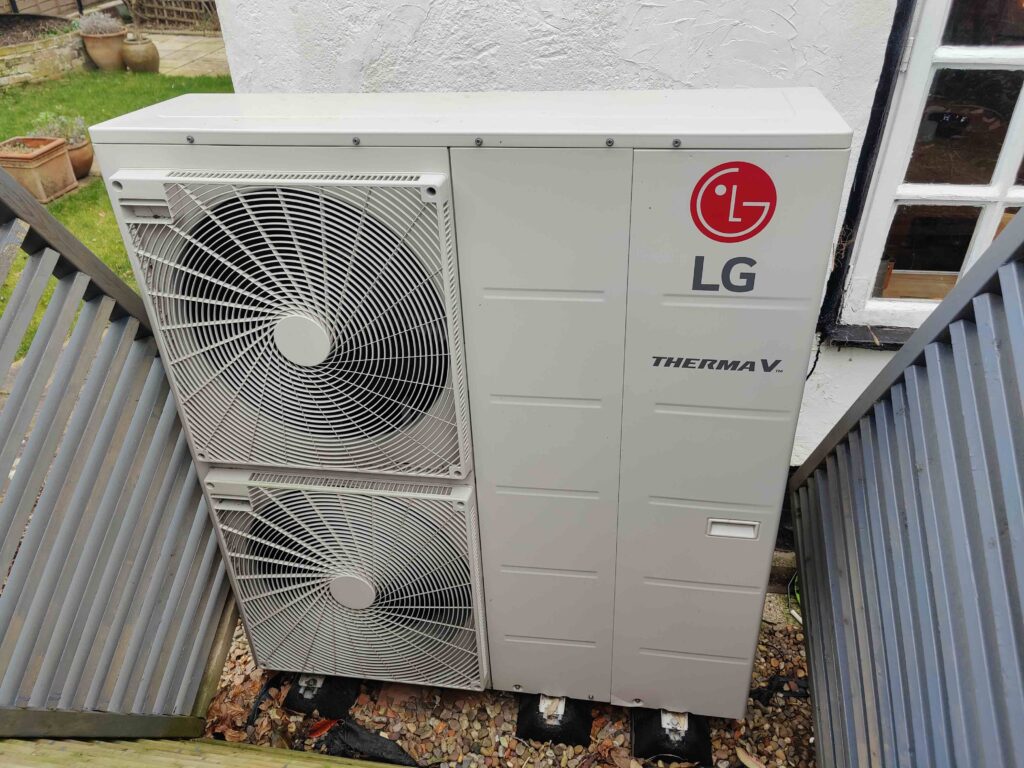
PAS selected local fitters Barilla (https://barillafuture.com/pages/approved-installers) who organised the final paperwork as well as installation.
1. Paperwork: Registration for the Renewable Heat Incentive, the Government scheme that was available at the time. This guaranteed quarterly payments towards increased electricity costs for 7 years after installation. The RHI amount is calculated factoring in the type of ASHP and expected annual kWH usage of the property.
(Note: the current – March 2024 – equivalent scheme is now a £7500 payment towards ASHP installation)
2. Installation (see photos): The ASHP unit was positioned behind the rear elevation of the Kitchen. The hot water cylinders, 2 expansion tanks and associated electrical and main control unit were located in his cellar, with a portable room thermostat.
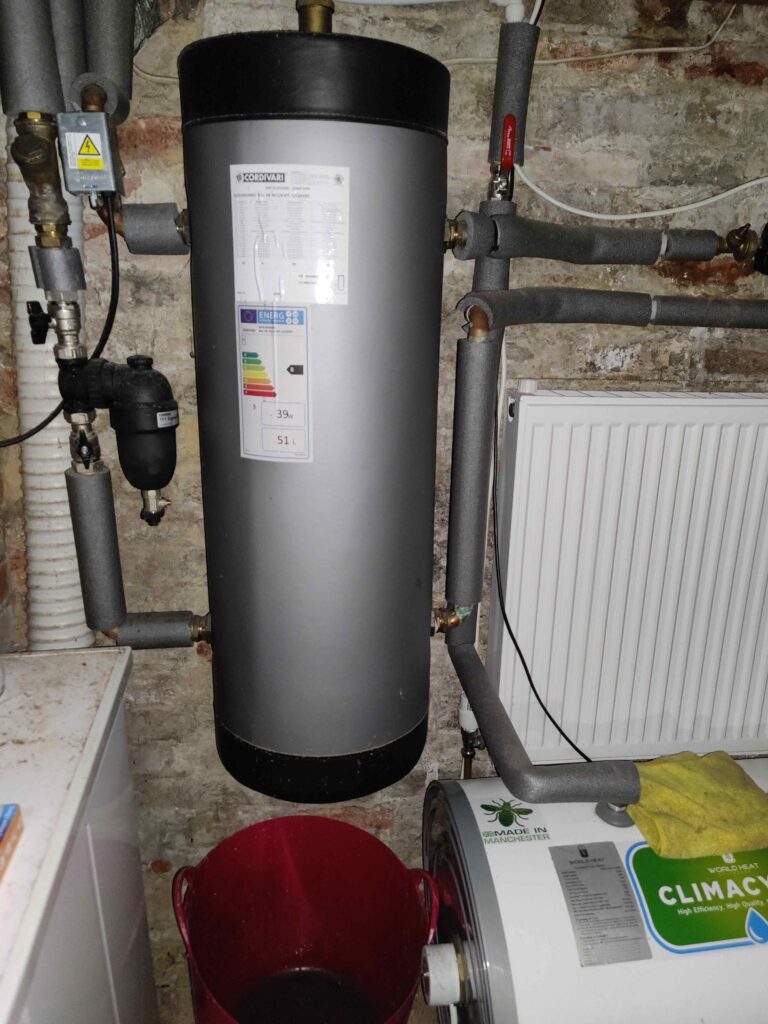
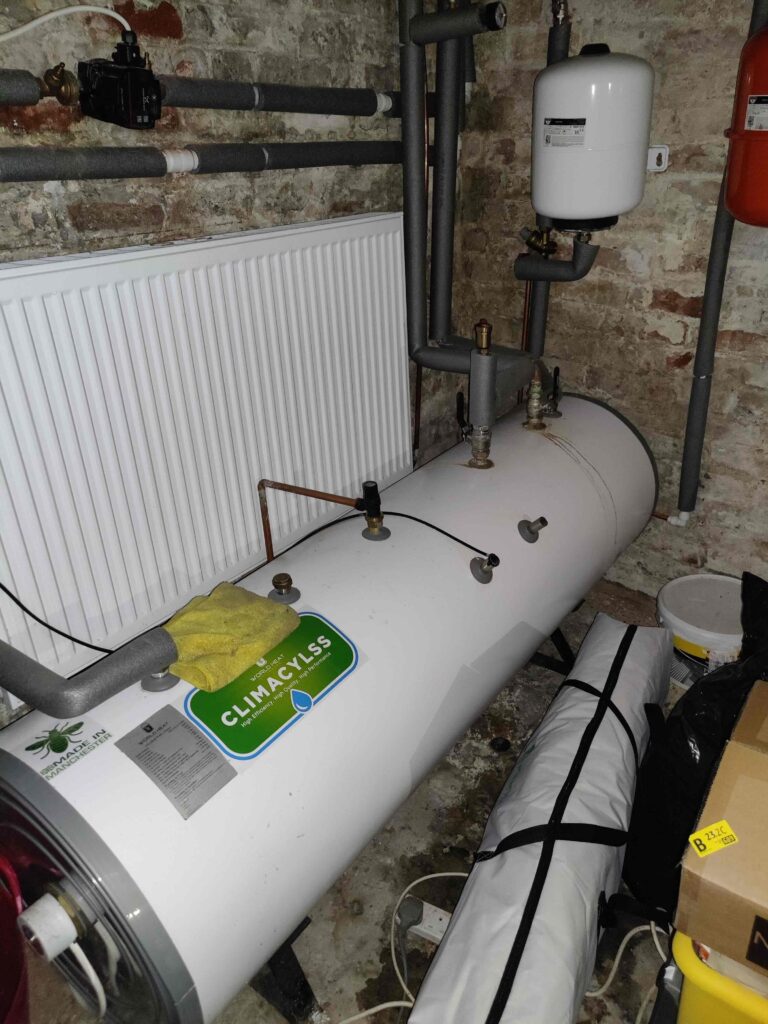
The overall installation cost: £20K if paid for outright, £30K on a finance deal.
How does the system work and how is it controlled
The system is set up to provide hot water on demand. It runs 4 heating cycles in winter, with an option to reduce to 2 in summer, controlled by the portable room thermostat. The thermostat is normally set to 17-19 degrees in winter, or 20-21 in very cold weather. This can also be manually overridden to have the heating on constant. In summer, the thermostat temperature is reduced to 14-16 degrees and just runs 2 daily heating cycles to provide the hot water on demand, heated to 52 degrees which is sufficient to prevent legionella.
The house is now continuously warm, and further improvement was gained by installing secondary glazing to the front elevation windows. They used Anglian Windows who were very good. Charlie intends to install secondary glazing to the rear elevation windows at some stage (in the younger part of the house) to further improve heat retention.
Running costs
These are smaller over the summer months, as of summer 2023 approximately £100-150/month. Costs are higher over the winter months, as of autumn/winter 23/24 approximately £500-£600/month electricity. For comparison, prior to installing additional insulation, Charlie said his 1200L oil tank cost approximately £1,500 to fill on average per annum between 2009 to 2019, and he estimated they used approximately £1,000 Electricity per year giving an overall cost of £2500 per year on electricity and heating.
Their electricity provider switched from Bulb to Octopus, when Octopus took over Bulb in early 2023. He highly recommends Octopus, who provide a good user-friendly website, good customer service, and regular energy saving schemes.
Annual servicing is provided by Vomax https://vomaxenergy.co.uk.
Breakdowns/Issues:
2020: the printed circuit board faltered. It transpired that there was a fault across the whole 2019 model LG THERMA V line. The circuit board was replaced very quickly via an installer arranged by PAS (Project Air Source).
2021: The heat exchanger cracked after a very cold winter and failed to work effectively. Internal issues between PAS, the original installers and LG, resulted in Charlie liaising directly with LG who arranged for a new 2021 THERMA V ASHP installed free of charge under the manufacturers warranty, using the original installers. LG’s customer service in the matter was excellent. The replaced ASHP has worked well to date with no issues.
Charlie’s advice: Avoid a third party agency and go directly to the ASHP manufacturers, and use them and their appointed installers.
Bottom line: The ASHP works well, they never run out of water and the house is warm. However, this was a ‘retro-fit’ into an existing property, in this case an old Listed property which has also been deemed ineligible to have a viable number of solar panels, and currently not all the windows have secondary glazing. Being fully electric has increased his costs compared to oil heating and separate electricity, compounded by current electricity prices, although these appears to be gradually reducing. However, despite the increased costs, he understands that having an ASHP will make selling the property in the future easier, as it is expected that domestic heating oil will become an obsolete option, and it’s good for helping to decarbonise the country.